Efficient Battery Thermal Management Systems for EV
Abstract
Energy and power density constitute two main performance parameters of an electric vehicle battery pack, representing the range and acceleration of the vehicle. This project focuses on improving the energy density of the battery pack for better overall performance of the electric vehicles; two wheelers in particular. This is achieved by improving the effectiveness and efficiency of the battery thermal management system for reducing the cell capacity degradation caused by temperature effects. An air-cooled cylindrical battery pack is considered for this purpose and different cell arrangements and flow patterns are studied for reducing the temperature variation across the cells and also the peak cell temperature, for minimizing the extent of degradation during charge discharge process. The effect of cell pack configurations and type of coolant used is also studied. The degradation studies are done through numerical simulations. For this, a coupled 1-D electrochemical and 2-D/3-D thermal model of the battery pack is used for the numerical simulations. This is further coupled with a capacity fade model to account for cell capacity degradation.
Objectives
To numerically model and design a parallel cooled air-based thermal management system having the following characteristics:- Minimum peak pack temperature
- Minimum cell-to-cell temperature difference
- Low energy requirement
Methodology
The numerical model of BTMS is set up in COMSOL Multiphysics software. The model consists of two parts : a 1-D model of cell for simulating the electrochemical process and a 2-D/3-D model of battery pack with casing representing the BTMS for simulating the thermal and fluid flow processes. The 1-D and 2-D/3-D models will be coupled together by means of average heat generation rate and maximum cell temperature. The 1-D model will simulate the charge-discharge process of a cell and will provide the volume-averaged cell internal heat generation time profile as an output result. This data will be used in the 2-D/3-D thermal model as an input for heat generation source in the cell for simulating the fluid flow and thermal heat exchange process. The output of the 2-D/3-D model will be the temperature distribution in the battery pack and it will be used to calculate the maximum temperature of all the cells constituting the pack. This maximum cell temperature value will then be used as an input for the 1-D electrochemical model. Maximum temperature is being used here to consider the worst-case scenario of battery pack life which will provide us with the minimum battery pack life, giving a lower bound value. Specifically, the 2-D model will be utilised to analyse different cell arrangements in a full scale battery pack. The 3-D model will be used to analyse the effect of heat generation in busbars on the pack performance, when the cells are connected in different configurations. Cell temperature can affect the capacity degradation and the discharge process of the cell, hence it is being given as an input to the 1-D model. By using this coupled model, different types of cell arrangements will be analysed for appropriate external inlet air conditions. The aim will be to minimise the cell capacity degradation rate by improving the airflow pattern and hence the heat dissipation rate.Conclusion
A battery pack made from 26650 type of Li-ion cell performs better than that made using 18650 or 21700 cell type in terms of capacity degradation and charge-discharge cycle time period. By arranging the cells in tapered manner, lower capacity fading, maximum cell temperature and maximum cell-to-cell temperature difference is obtained which enhances the pack cycle life and the performance of BTMS.Some of the Simulation Images
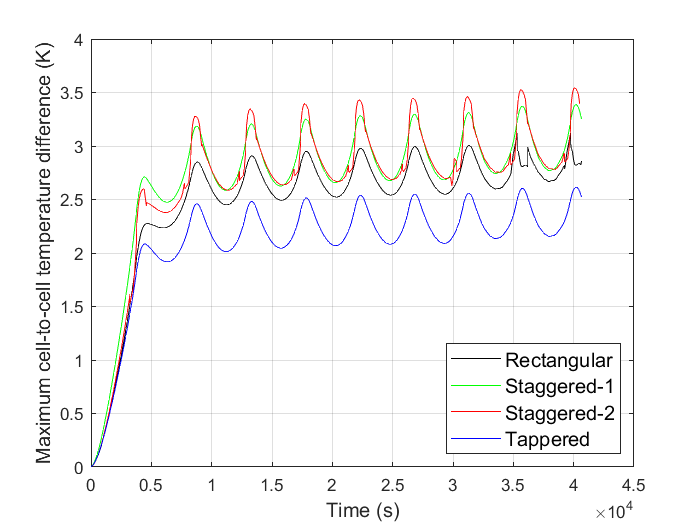
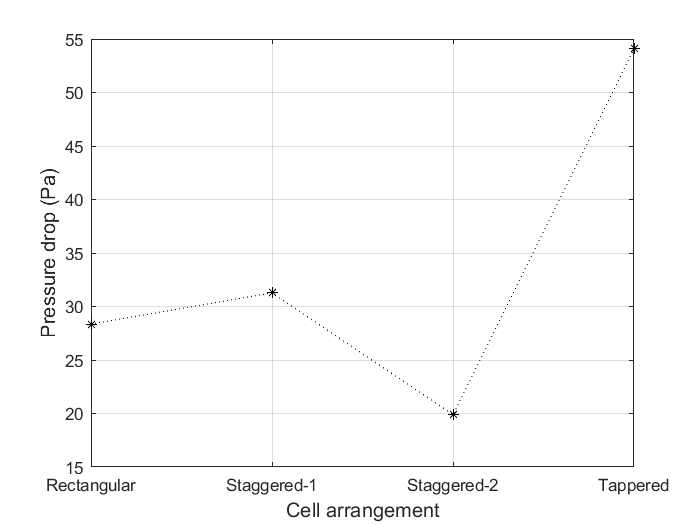
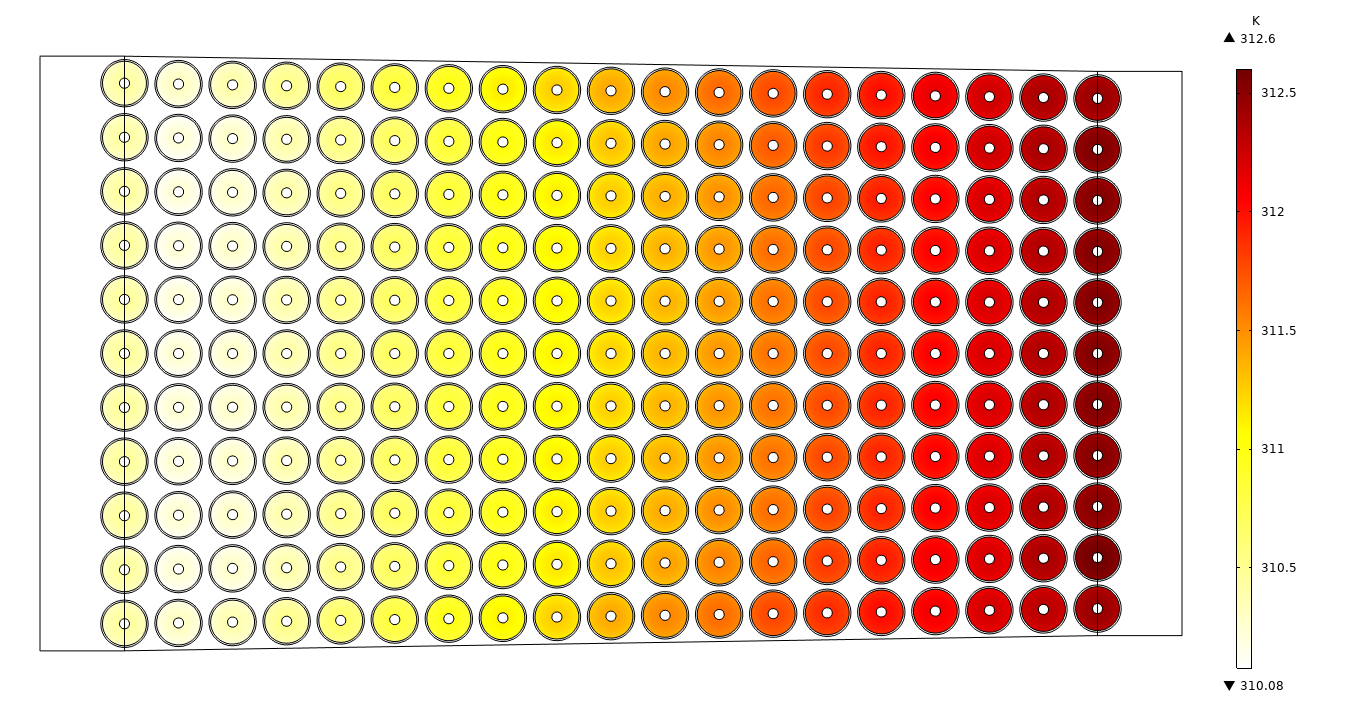
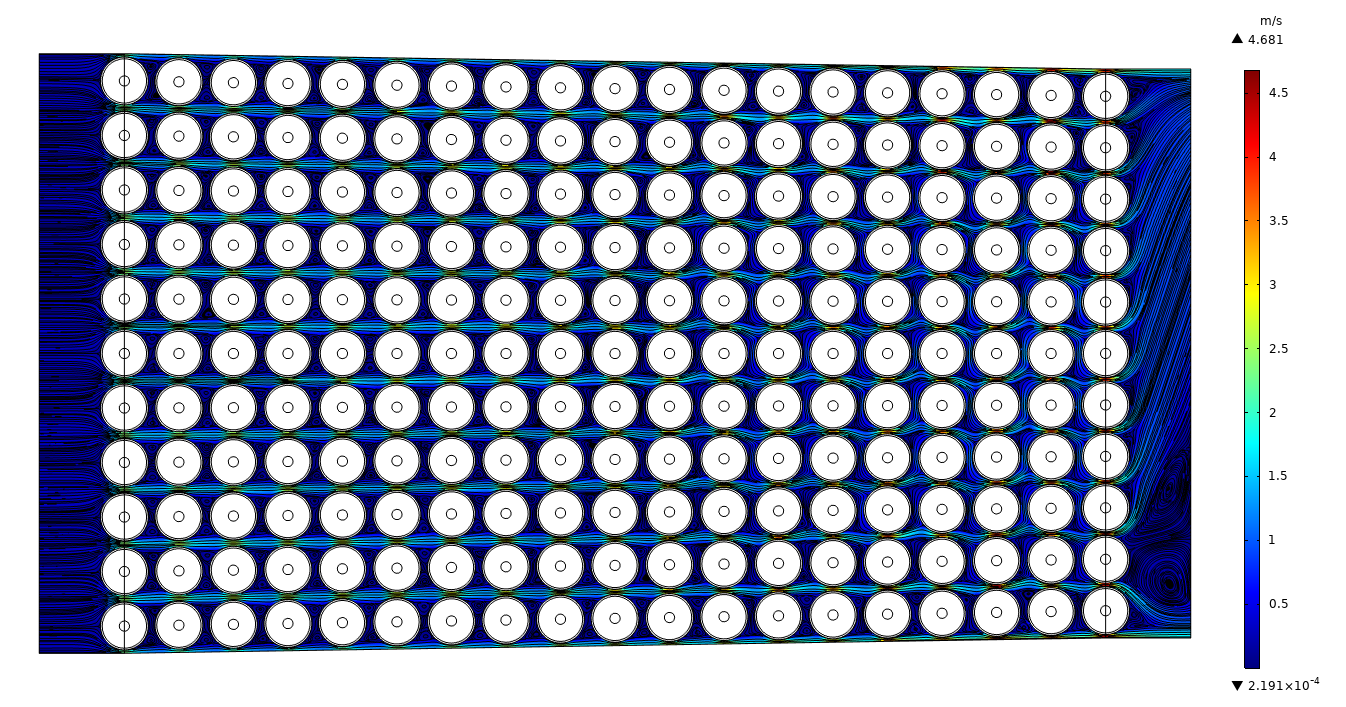
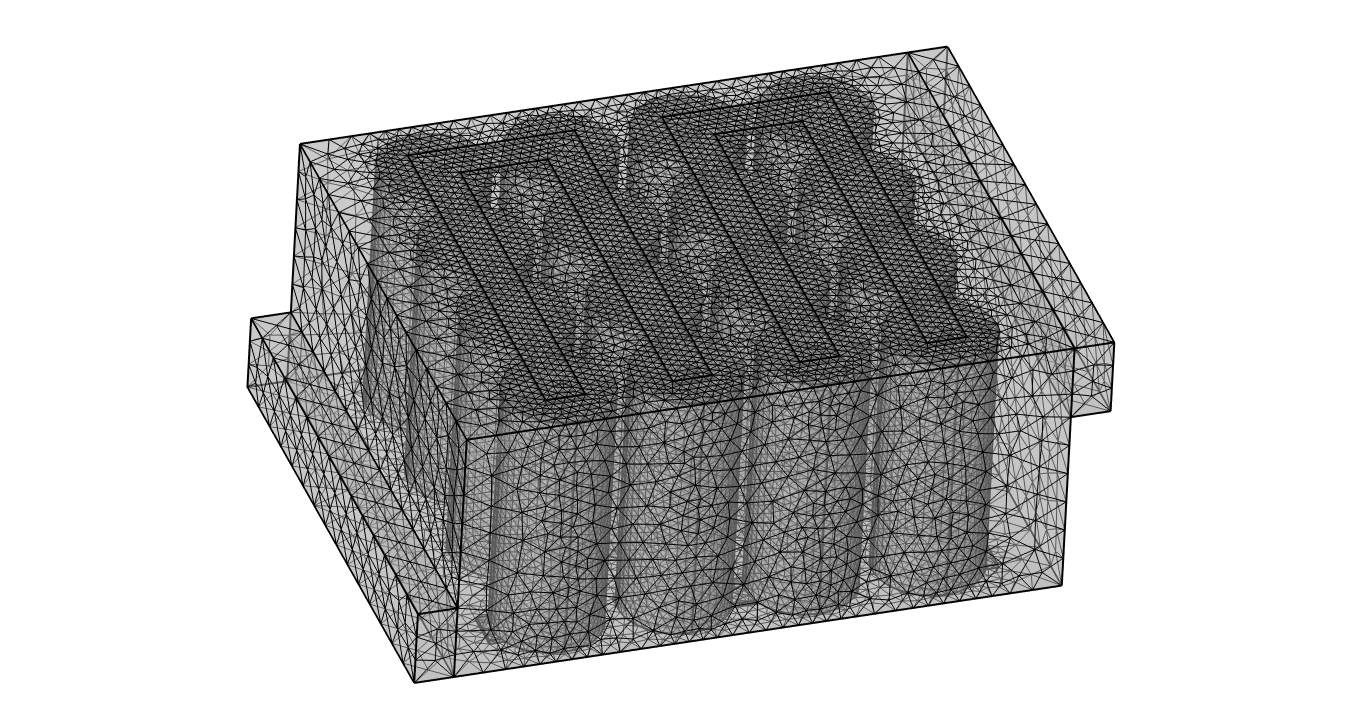
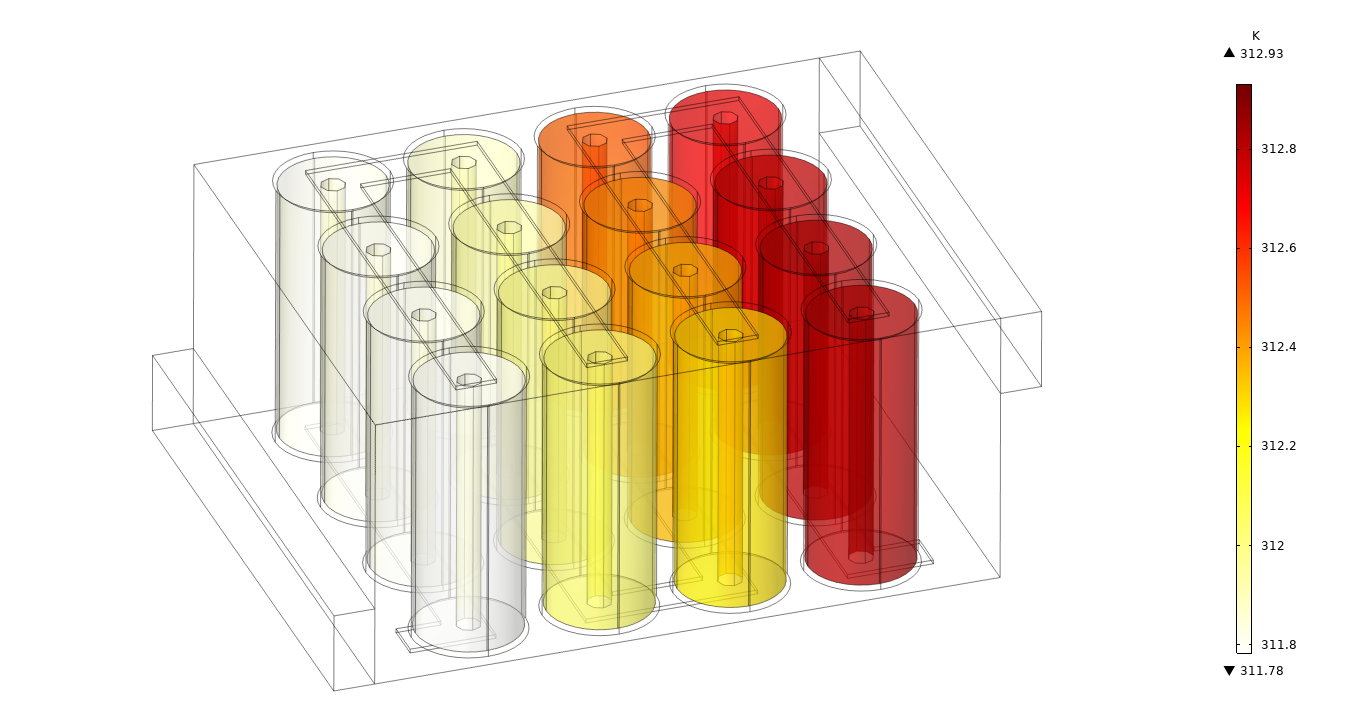